On November 29, an article titled “Fatigue-resistant high-performance elastocaloric materials made by additive manufacturing” was published in Science by the team of Dr. Hou Huilong, Associate Professor of the School of Aeronautic Science and Engineering and the lead author of the research.
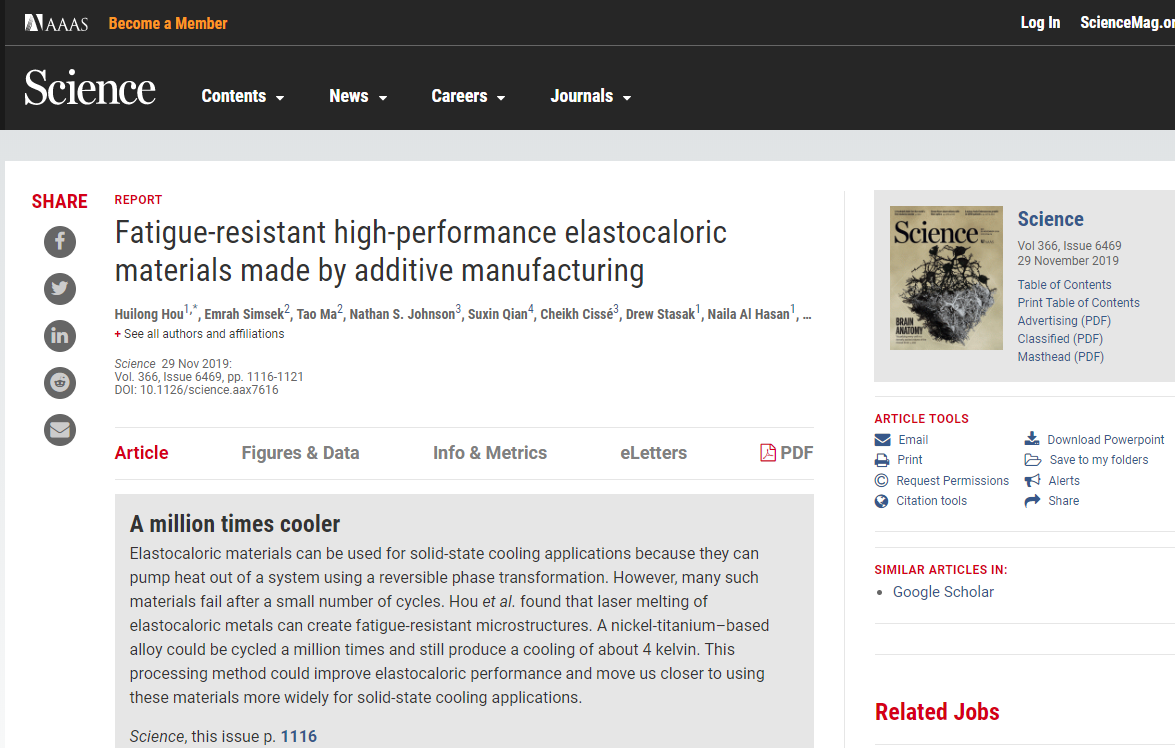
Space cooling and refrigeration account for about one fifth of the electricity consumption worldwide, leading to the rapid development of more efficient and environment-friendly cooling technologies and growing attention paid to solid-state (magnetocaloric, mechanocaloric, electrocaloric, etc.) cooling techniques. As a form of mechanocaloric cooling, elastocaloric cooling can bring about heat absorption and release resulting from a reversible change of the symmetry of the materials’ crystal structure by exertion or removal of the stress field. The technology was invented in 2012 at the University of Maryland and ranked first among the 17 replacements of vapor compression refrigeration listed by the U.S. Department of Energy (DOE) in 2014 for its giant effects of latent heat. Meanwhile, relentless efforts have been made to develop elastocaloric cooling prototypes and elastocaloric regenerative heat pumps for practical use. An unsolved problem, however, was the hysteresis of elastocaloric cooling materials that could limit the efficiency of the cooling system and influence the stability of its performance in the long term.
What the research proposed was a solution to the problem, thermodynamically efficient and low-hysteresis elastocaloric cooling materials produced by the means of additive manufacturing of nickel-titanium. Following a well-designed strategy of “technique-microstructure-property-performance”, the researchers made use of powder-feed laser-directed-energy deposition (L-DED) technique resulting in a local melting of metal powders followed by rapid solidification and adjusted the proportions of elemental powders to form nanocomposite microstructures composed of binary NiTi alloy matrix and a Ni3Ti intermetallic phase. The materials produced in this way showed extremely small hysteresis and featured an efficiency improved by a factor of four to seven as well as repeatable elastocaloric cooling performance over 1 million cycles.
The research revealed the interaction mechanism between the binary NiTi alloy matrix and the Ni3Ti intermetallic phase through a micromechanical model and in situ synchrotron x-ray diffraction experiments. Based on experiments, it obtained a correlation of hysteresis as a fraction of input energy to the cycles to functional failure and found that the correlation could also apply to other caloric materials, first providing scientific evidence concerning the manufacturing, selection and engineering design of long-life caloric materials. The research, therefore, was of scientific and technological significance for developing highly-efficient and stable solid-state cooling techniques. In addition, the additive manufacturing of elastocaloric cooling materials enabled distinct microstructure control of high-performance metallic refrigerants with long fatigue life, and the Ni–Ti–based elastocaloric material produced in the research demonstrated the potential of additive manufacturing in optimizing solid-state cooling techniques.
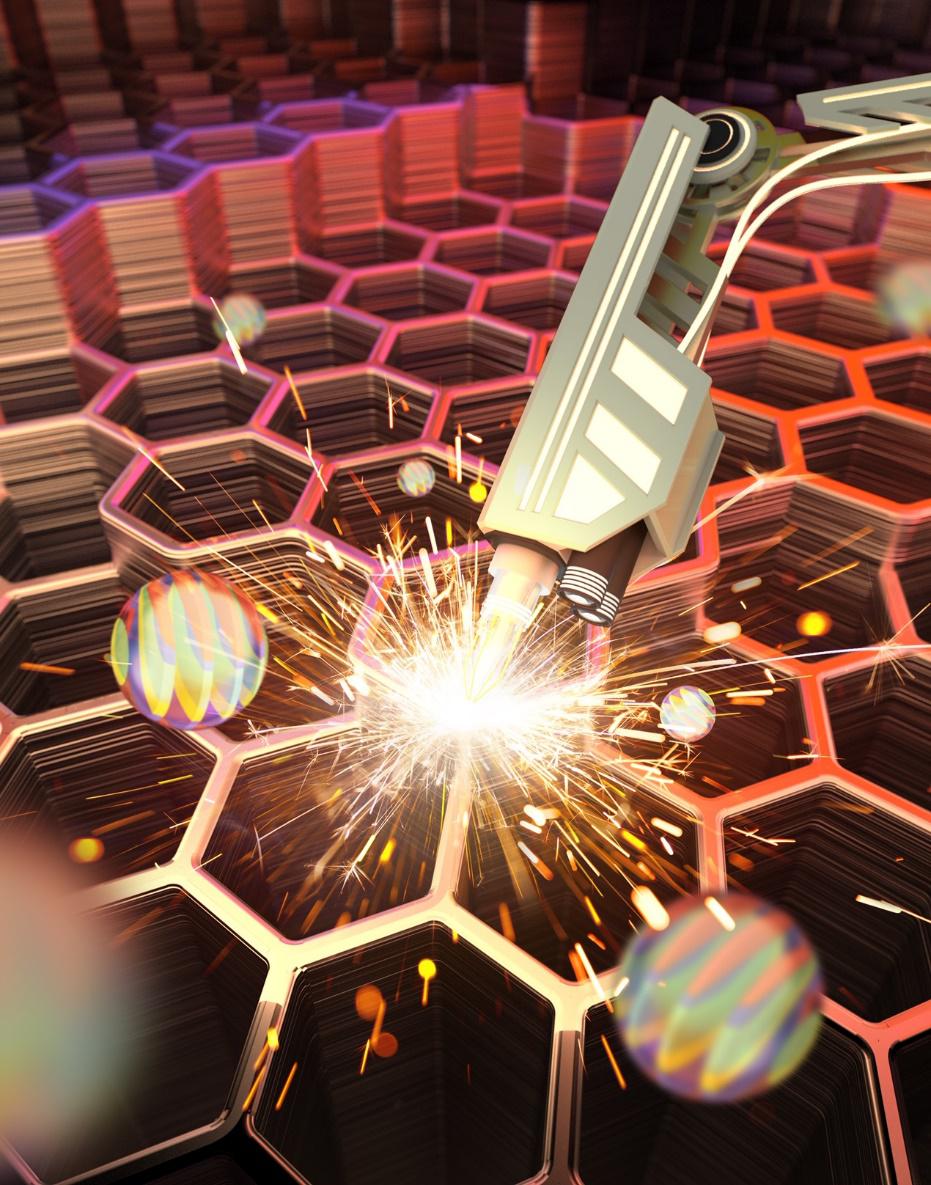
This image shows how fatigue-resistant high-performance elastocaloric materials can be made by additive manufacturing. A powder feeder provides a near-eutectic mix of elemental powders and the laser offers energy (upper right). The mixed powders form a molten pool under laser light and different parts of the component take shape as the molten pool move around (middle). In this way, the component is formed in the shape of a honeycomb and with a required height (background).
The research represented the joint efforts made by Dr. Hou, who joined Beihang in September this year, and his collaborators when he was still at the University of Maryland. It was funded by the Advanced Manufacturing Office and the Office of Science of DOE, the National Science Foundation, etc. Its follow-up study will be conducted at Beihang University to serve the national needs for special cooling technology used in aircraft and spacecraft. The future work will involve participants from characteristic majors of the School of Aeronautic Science and Engineering (Structural Strength of Aircraft and Ergonomic and Environment Engineering), the School of Materials Science and Engineering, the School of Mechanical Engineering and Automation and other relevant institutions at home and abroad.
More information of the research:
https://science.sciencemag.org/content/366/6469/1116
Reported by Xing Yufeng and Yuan Weixing
Reviewed by Lin Guiping
Edited by Jia Aiping
Translated by Li Mingzhu