The team of Professor Chen Yuli from the School of Aeronautic Science and Engineering published their research findings online titled “3D Pixel Mechanical Metamaterials” in Advanced Materials on May 10. An innovative material design strategy named mechanical pixel (MP) array design is proposed in the paper aiming to break the limit and exploit more potentialities of metamaterials.
Usually constructed with periodically interconnected building blocks (also called “meta‐atoms”), metamaterials have unprecedented properties and functions such as auxeticity negative compressibility, programmability, and shape‐reconfigurability that facilitate the development of advanced devices and machines.
However, their interconnected building structures limit their applications at the same time. The kinematics of the meta‐atoms are highly coupled and mutually constrained, which hinders large local deformation between the meta‐atoms. In addition, when encountering external loads, the passively induced shear deformation may lead to damage of the materials.
It is noteworthy that high deformation flexibility and load‐bearing robustness of the materials are of great importance and in urgent need in many applications, especially when the materials need not only to transform actively to adjust to circumstances but also to withstand extreme external loads, such as automotive armors, transformable robots, and morphing aircraft. Therefore, the means to gain more flexibility and robustness without sacrificing original performances poses a challenge for material and structure design.
The newly proposed 3D pixelated design strategy comes to the rescue. It is able to form and reconfigure 3D morphologies by tuning the heights (lengths) of the MPs in the array, which is similar to a screen that displays images by adjusting the colors of pixels.
It is first inspired by the spines of the hedgehog. Hedgehogs can erect their spines, which is of use not only to threaten and stab predators, but also to buffer the shock when falling from heights of more than 10m. Moreover, the damage to one spine rarely propagates to any other spines, which means the prevention of further destruction. That is the power of the array structure ubiquitous in nature, where the macroscopic deformation originates from the uncoupled deformations of the individuals.
Similar to the arrangement of hedgehog spines (Fig.1(a)), an array architecture design composed of parallel pillars is proposed. Periodically assembled in a patterned framework, these pillars should have the characteristics of morphing and absorbing mechanical energy. One of the most excellent candidates with these properties is the multistable element architected by bistable units in series (Fig. 1(b)). It can switch among its multiple stable shapes and absorb energy via fully reversible elastic deformation. Moreover, it has a greater tunable mechanical response, larger deformation amplitude, and a greater number of stable shapes compared to other strategies, such as shape memory material and foldable origami. Therefore, the mechanical multistable element is adopted here. To guarantee the kinematic decoupling and the load capability of the pillars, only the axial deformation is allowed because bending is generally inefficient in load‐bearing. Thus, the metamaterials can deform without shear constraint and present abundant 3D configurations.
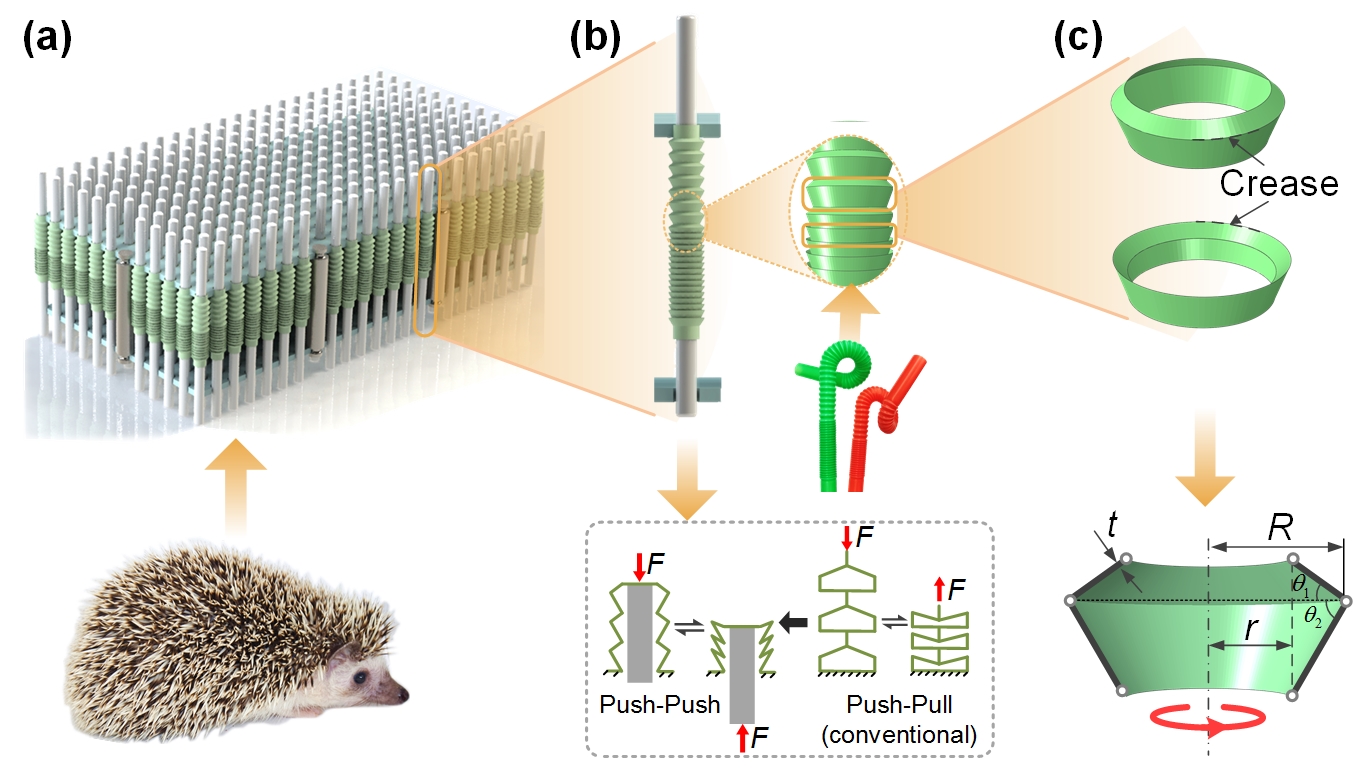
Fig. 1 The design scheme of 3D pixel mechanical metamaterials
Since the pillars in the array are very similar to the pixels on a screen, i.e., the former form 3D morphologies by varying heights (lengths) while the latter display 2D images by tuning colors. They are defined as mechanical pixels (MPs).
In the meanwhile, inspired by the “flexible drinking straw”, the team implement the design concept in an easily assembled prototype. As the meta atom, the basic unit of the straw-like structure has two required stable states, deploy and retract (Fig. 1(c)), and it can be described by five independent geometry parameters, diameters R and r, the truncated cone angles θ1 and θ2, and the thickness of the wall t (Fig. 1(c)).
Moreover, mechanical design and property prediction for the metamaterials are both greatly simplified due to the pixelated design. For a piece of the 3D pixel metamaterial with m n‐unit MPs, the number of programmable displacement–force curves increases from n+1 to 2m∙n+1, and the number of stable morphologies grows from n+1 to at least (n+1)m. This strategy can be used to enhance the merits and further excavate the potential of versatile metamaterials (Fig. 2).
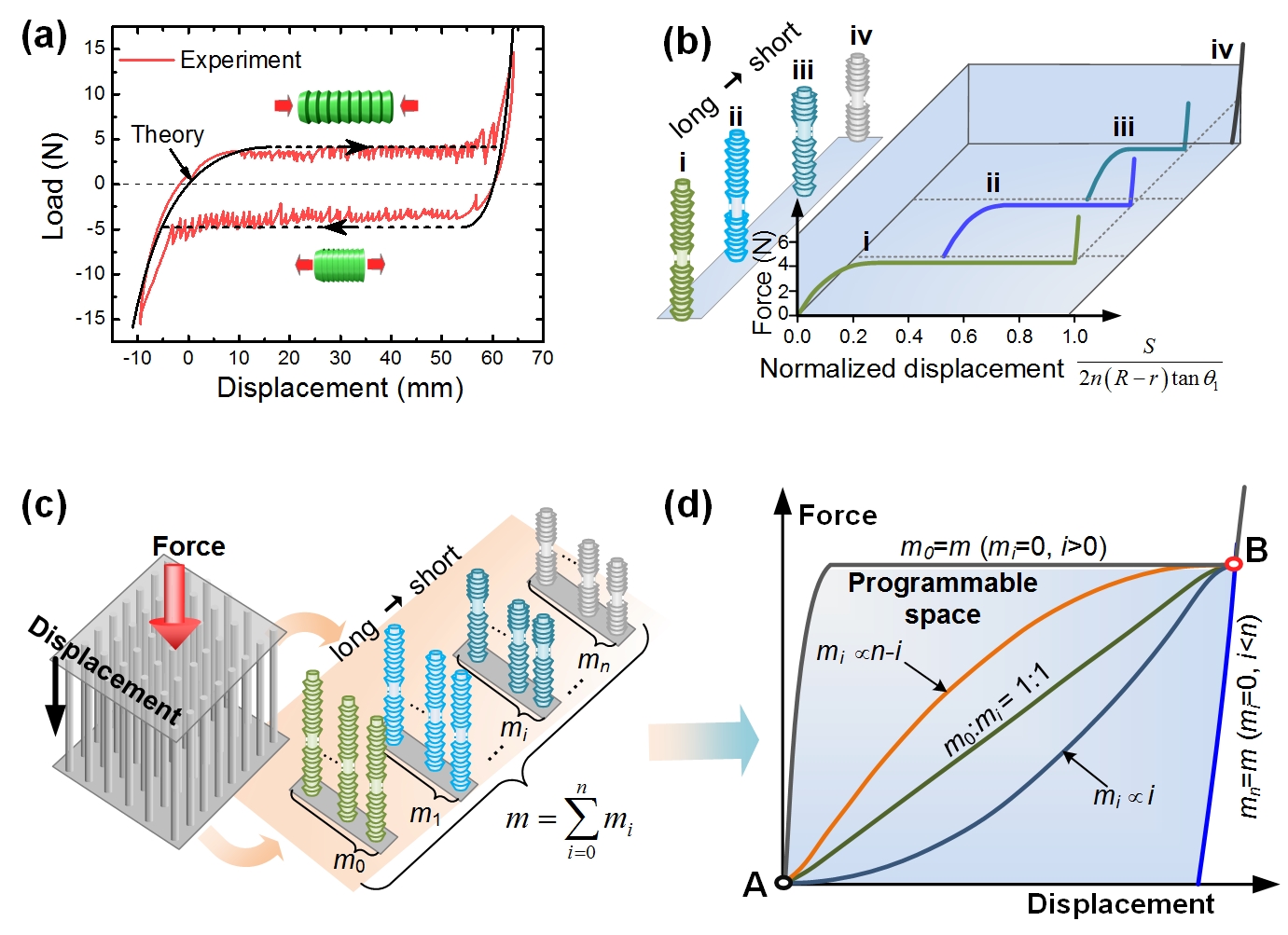
Fig. 2 The mechanical behaviors of 3D pixel metamaterials
In addition to actively tuning their shapes to program the loading curve, the metamaterials can also be actively morphed to adapt to different environments and applications (Fig. 3). It is expected to be applied to design and fabricate versatile metamaterials or metastructures in many fields, ranging from transformable machinery and robots, to reusable energy absorbers for car accidents and stable landing cushions for recyclable spaceships and rockets, and to material constitutive simulators and mechanical information preservation devices. Additionally, it can be used to enhance the merits and further excavate the potential capabilities of other versatile metamaterials.
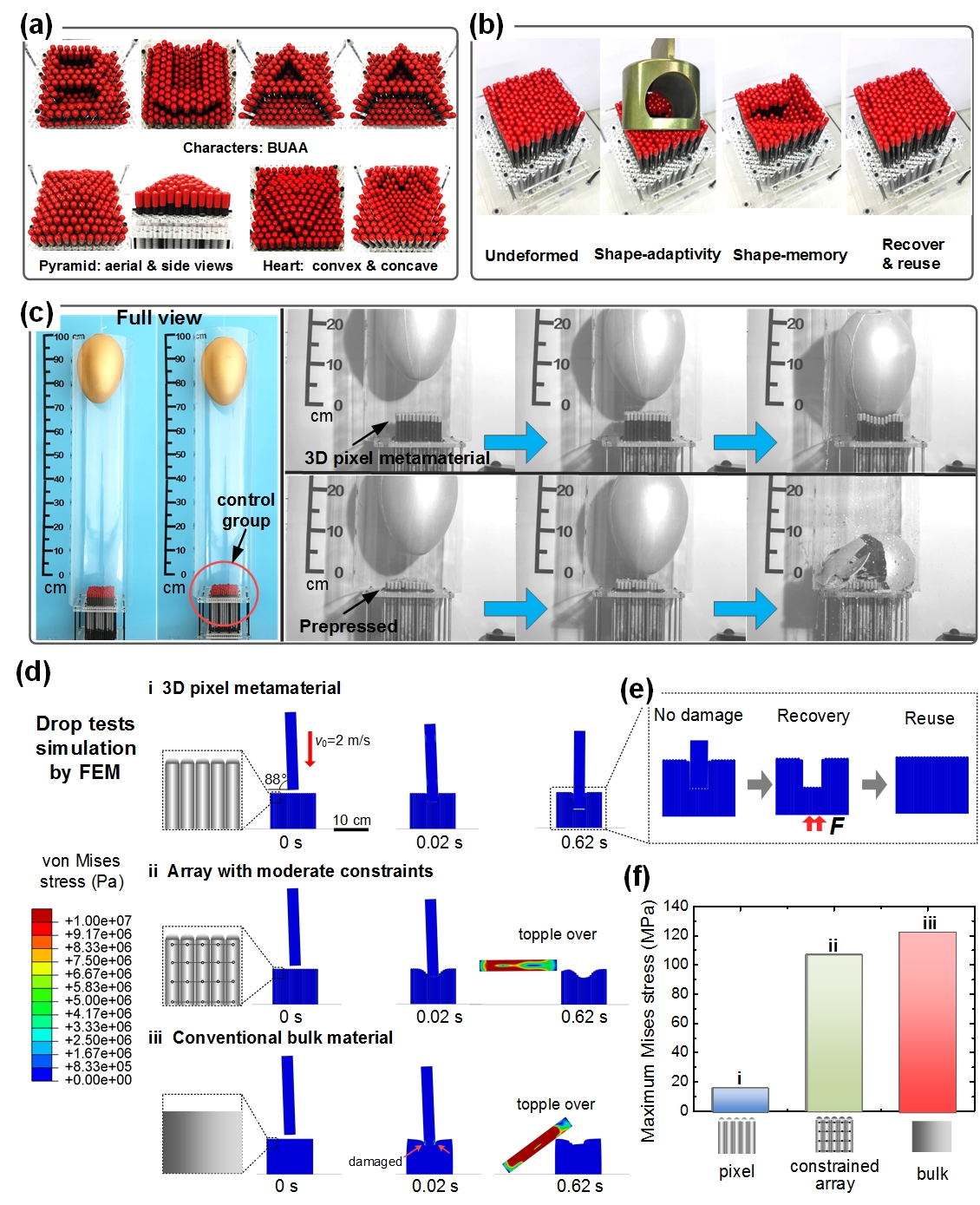
Fig. 3 Shape reconfiguration and impact resistance of 3D pixel mechanical metamaterials
The first author of the paper is Doctor Pan Fei, and the correspondent author is Professor Chen Yuli. Professor Yang Jialing of Beihang University and Professor Liu Bin are the co-authors.
The program is funded by the National Natural Science Foundation of China, the New Century Excellent Researcher Award Program by Ministry of Education of China, and Beihang Youth Talents Program.
Reported by Lin Xin
Reviewed by Lin Guiping
Edited by Jia Aiping
Translated by Li Siying