A research team from the School of Mechanical Engineering and Automation reviewed the latest advances in the field of tensegrity metamaterials for soft robotics in a focus article published in Science Robotics on August 26. Prof. Wen Li was the first and corresponding author of the article, and its co-authors were Prof. Ding Xilun and Dr. Pan Fei, a postdoctoral researcher.
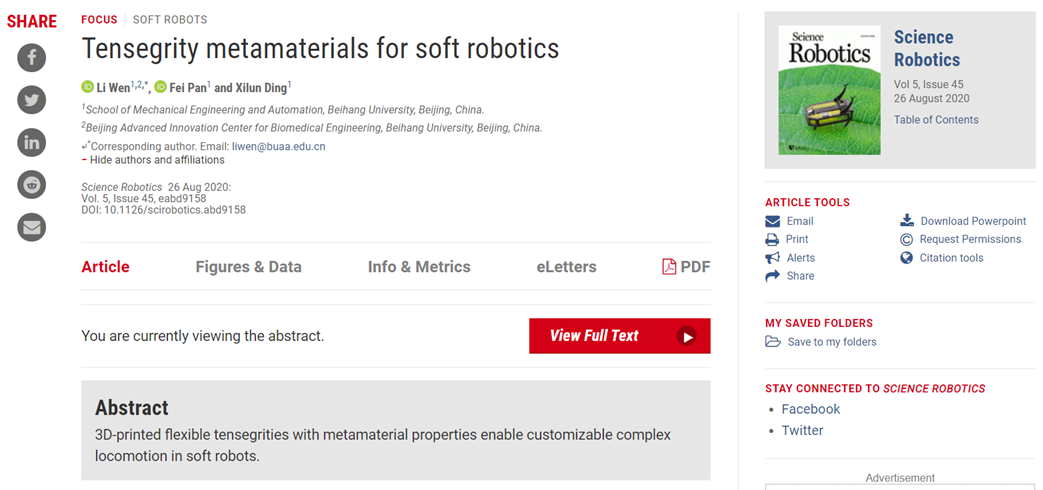
Fig. 1 The focus article published in Science Robotics
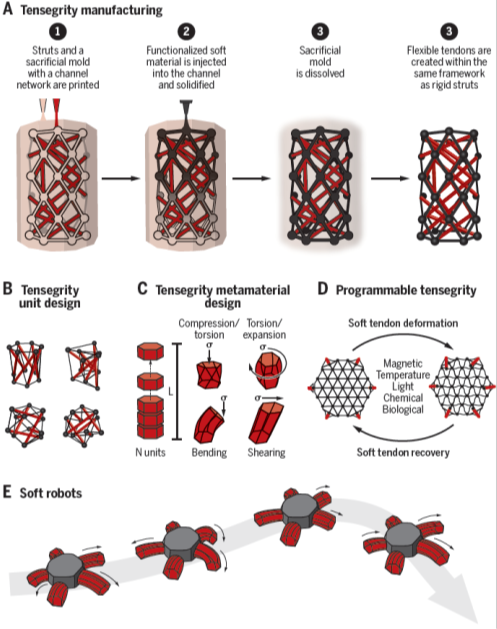
Fig. 2 A tensegrity metamaterial approach to soft robotics
Since “tensegrity” was defined by Buckminster Fuller in the 1960s, researchers have identified the widespread existence of tensegrity structures in cytoskeletons, musculoskeletal systems, etc., and applied it to engineering structures and mechanisms in architecture, sculpture, space exploration and so on. It enjoys great prospects in robotics for its combination of structural integrity and flexibility as well as high structural mobility and robustness.
Although soft robotics, a branch focusing on bio-inspired robots that can interact safely with humans, has become a hot topic at the intersection of robotics, mechanics and material science, it still faces challenges regarding materials and structural design if complex functions like flexible and precise movement, efficient load-bearing capacity and high adaptability are to be equipped. Such challenges can be tackled with the application of tensegrity structures, but researchers still need to solve issues like how to rapidly manufacture tensegrity structures and how to enhance the mechanical performance of soft robots with such structures.
From this perspective, the Beihang researchers reviewed and analyzed traditional tensegrity structures, and then introduced a recent study published in Science Robotics (https://doi.org/10.1126/scirobotics.aay9024). The research proposed an approach that can rapidly produce three-dimensional tensegrity structures. This method enabled rapid integrated manufacturing of magnetic soft materials with rigid beam elements and processing of tensegrity metamaterials with features like compression-torsion/torsion-expansion coupling and programmable mechanical properties. According to the Beihang researchers, this method successfully combined a functionalized soft tendon material with isolated rigid beams and paved the way for fabricating programmable tensegrities across various scales and materials.
The team also looked ahead into the future research directions and prospects of soft robots made of tensegrity metamaterials. As this approach leaves wide space for design with soft materials, structures and mechanisms, it can significantly improve the adjustment and control of soft robots’ drive, transformation and mechanical properties. Future researches may apply more analytical and algorithmic design of flexible structures with the use of tensegrity metamaterials, or develop theoretical models based on multi-scale mechanics and calculation models based on machine learning to enable customizable complex transformation in soft robots. To improve the flexibility and adaptability of soft robots, smart materials can be adopted, and future robots may move without cables and be activated by light, heat or chemical stimuli. Tensegrity metamaterials are also expected to provide more possibilities for robots used for biological engineering, exploration and survey, medical service and so on.
More information:
https://robotics.sciencemag.org/content/5/45/eabd9158
Reported by the School of Mechanical Engineering and Automation
Edited by Zhang Boyang
Designed by Wu Haojing
Reviewed by Qin Nan
Produced by General Editorial Office of Official Site (GEOOS)
Please send contributions to geoos@buaa.edu.cn