Recently, the team of Prof. Luo Sida from the School of Mechanical Engineering & Automation of Beihang University successfully fabricated freestanding and large-size graphene papers using the Laser Induced Graphene (LIG) technology. The latest research findings are published in prestigious research journals Small (IF: 9.598, Q1) and Carbon (IF:7.082,Q1). Wang Yanan, a doctoral student of Beihang and Wang Yong, a graduate of Beihang are the first authors of the two articles published in Small and Carbon respectively. Prof. Luo Sida is the only correspondent author and Beihang is the only correspondent affiliation.
The graphene paper’s advantages and its preparation methods
The freestanding graphene paper (GP), a novel architecture with the assembly of 2D layered carbon, has aroused tremendous research interests due to its intriguing properties, including self-supportiveness and robustness, lightweightness and high porosity, excellent electrical and thermal conductivity, etc. The multimodal characteristics make it highly important as the building block to assemble a wide range of smart devices and structures, from sensors and energy devices to biomimetic scaffolds and nanocomposites. However, it is hard to achieve commercial fabrication of GP by the self-assembled method in the liquid phase, a traditional GP fabrication method featuring high cost and low efficiency. To address the problem, James Tour, an American chemist, proposed the LIG technology in 2014. The fabrication process assisted by the new technology features low cost, ease of operation and high efficiency. However, the fabrication of freestanding and large‐size GPs through LIG technology remains a research gap in this field, which limits the applications of LIG technology. Prof. Luo’s group identified the issue and conducted a series of research to find feasible ways of fabrication.
Inspired by a small clue
In an attempt to produce LIG based sensors using polymer films, Prof Luo’s group found that the LIG structure converted from polyimide (PI) paper is free from serious shape distortion and has greater electrical conductivity. Inspired by this, Prof. Luo started to guide his team to find the method of directly converting a piece of commercial PI paper into a freestanding film-like ensemble with the entire body of black LIG, which remains to be distortion-free, electrically conductive and mechanically stable in the process.
Finally, Prof. Luo’s team successfully fabricated freestanding and large-size GPs using the Laser Induced Graphene (LIG) technology. According to their research, the decisive factor of PI paper is the unique spatial arrangement of fiber network with free spaces, which is critical for high-efficient absorption of photothermal energy and formation of graphitized structure without intense shape distortion. The utilization of PI paper also helps avoid many other processing problems such as stress concentration, cancellous structure, damage and out-of-focus blur. With the optimized protocol, the size of laser‐induced graphene paper (LIGP) is up to 40 × 35 cm2, which to our knowledge is among the largest GPs fabricated in lab. Besides, the flexibility and toughness of the GP material render it possible to be cut and trimmed into complex structures with scalable sizes under the assistance of high power lasers. The GP material can also be cross-linked with advanced industrial material such as resins.
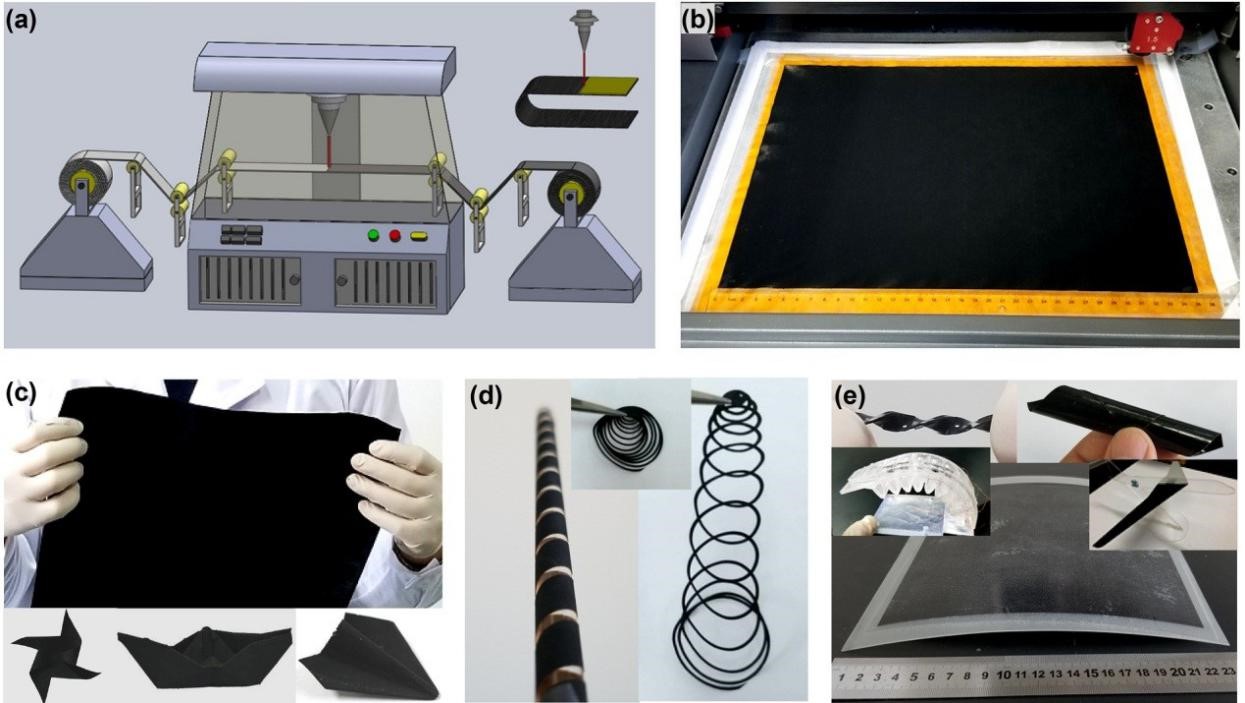
Fig. 1 Concept, preparation, demonstration, and microstructures of LIGP
Based on a comprehensive research on understanding the processing–structure–property-performance relationship, Prof. Luo’s group discovered that the laser-induced GP has good mechanical, electrical, thermal and electrochemical performance, which renders them unique for assembling smart structures such as wearable hand gesture recognition device, robotic motion detectors, water-oil separators and antibacterial interface as well as resin matrix composites widely used in aviation industry with properties of flame retardant, deicing and structural integrity assurance. Therefore, LIGP will be a promising commercial material in the future.
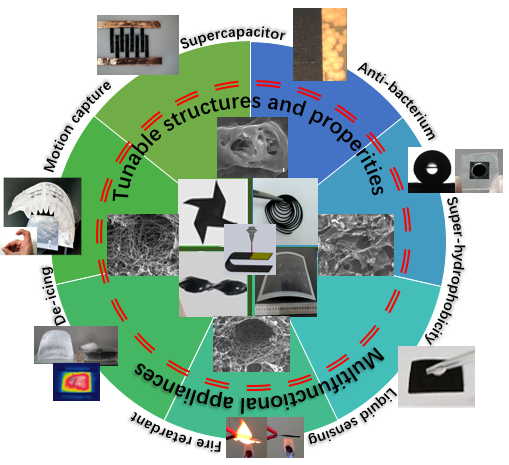
Fig. 2 Tunable structures, properties and multifunctional applications of LIGP
Hopes and aspirations for the future
As for the future plan, Prof. Luo said that he and his team would continue to focus on the LIG technology, exploring its possible applications and expediting its commercialization, roll-to-roll manufacturing, and multidisciplinary uses in the future.
“In scientific research, there will always be a huge gap between original plans and the actual outcome. However, it is often the unpredictable outcome that inspires new ideas,” said Prof. Luo at the end of the interview. When conducting researches, scientists should attach importance to every single experimental result because an unexpected breakthrough may be achieved based on a seemingly unusual finding. Additionally, Prof. Luo noted that we should have an international vision and keep abreast of the frontier technology so that we can take advantage of them to make a new breakthrough.
Conclusions
The LIG technology proposed by Prof. Luo’s team as well as its cost-effective method for large size preparation, tunable properties and multifunctional applications are instructive for the commercialization and large-scale preparation of macroscopic graphene materials. In the next stage, Prof. Luo’s team will further study the LIG technology based on the existing research findings and explore its multidisciplinary applications. They are expected to make greater breakthrough in this field in the future.
The research is supported by the Young Scientists Fund of the National Natural Science Foundation of China, the Innovation Fund of the National Business Aircraft Manufacturing Engineering Technology Research Center and the Aeronautical Science Foundation of China.
The articles are available at :
https://doi.org/10.1002/smll.201802350
https://doi.org/10.1016/j.carbon.2018.07.014
Planned and Edited by Shen Yifan
Interviewed by Shen Yifan, Xiong Ting and Tan Lisha
Designed by Wang Chenyan
Translated by Xiong Ting
Reviewed and Released by GEOOS
Special thanks to Prof. Luo Sida
Please send contributions to geoos@buaa.edu.cn